Large-sized Touch Panel for Improved Operability
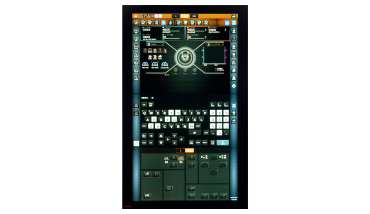
A 21.5-inch touch panel providing excellent visibility is adopted for better operating convenience during setup.
The 3-screen multi-display allows the operator to switch among screens depending on the operation purpose.
The home screen makes operation status information including the “start conditions”, “estimated time to machine stop”, “production progress” and “machine operating status” available on a single screen for more efficient checking.
In addition, traceability data is saved to track changes in the machining status of individual workpieces and other information to help run facilities smoothly.
The 3-screen multi-display allows the operator to switch among screens depending on the operation purpose.
The home screen makes operation status information including the “start conditions”, “estimated time to machine stop”, “production progress” and “machine operating status” available on a single screen for more efficient checking.
In addition, traceability data is saved to track changes in the machining status of individual workpieces and other information to help run facilities smoothly.
Shorter Loading Times
Installing a new loader system has increased the rapid traverse speed on all axes. The shortest loading time is 10% faster than on existing models, at 5.5 seconds. This increases productivity from workpiece supply to unloading.
The loader is available with optional “lightweight specifications”, where new materials are used in place of steel in the structure to increase speed and suppress vibration.
The loader is available with optional “lightweight specifications”, where new materials are used in place of steel in the structure to increase speed and suppress vibration.
Introduction of a New 3-axis Loader System
All the functions that simplify loader setup have been applied to a 3-axis loader system.
For improved operability, this system is centrally managed by using the same controller for the machine and loader.
The handle retrace function enables confirmation of operations with a high level of safety.
Incorporating the loader operations into NC programs allows flexibility in handling the operation and timing changes associated with workpiece setup changes.
These functions result in improved operability and productivity.
For improved operability, this system is centrally managed by using the same controller for the machine and loader.
The handle retrace function enables confirmation of operations with a high level of safety.
Incorporating the loader operations into NC programs allows flexibility in handling the operation and timing changes associated with workpiece setup changes.
These functions result in improved operability and productivity.
Reductions in Machining Defects and Energy Consumption
TAKAMAZ’s proprietary “Thermony®” thermal displacement correction system can predict the effects of changes in temperature on finish dimensions under various conditions of use and environmental conditions and apply corrections to curtail machining defects. In addition, adopting an air-cooled construction in the central part of the machine where heat sources are concentrated makes cooling water unnecessary, reducing running costs and energy consumption.
The machine has a hybrid slideway configuration, with a sliding friction guideway on the X axis for high rigidity and a roller friction guideway on the Z axis for high positioning accuracy. This improves machining performance and reduces consumption of lubricating oil.
The machine has a hybrid slideway configuration, with a sliding friction guideway on the X axis for high rigidity and a roller friction guideway on the Z axis for high positioning accuracy. This improves machining performance and reduces consumption of lubricating oil.